Advantages:
- High sensitivity and versatility for monitoring various parameters, suitable for applications like medical tapes, wearable electronics, and artificial eardrums.
- Reduced material waste and lower production costs through non-contact printing, eliminating mask cleaning.
- Scalable and efficient manufacturing with electric field-assisted processes, compatible with flexible materials for broad application.
Summary:
Traditional printing methods for flexible electronics, such as screen printing and digital printing, are time-consuming, require long drying times, and generate significant material waste. These methods also use complex combinations of materials and bonding agents that can degrade over multiple production runs. There is a need for more efficient, cost-effective, and environmentally friendly printing techniques for producing flexible electronics.
The innovative non-contact printing method described here uses electric fields to create sensors without the need for liquid inks or composite adhesives. This technology produces highly sensitive and accurate sensors with enhanced flexibility and a wide range of applications. The process reduces material waste, shortens production times, and lowers costs, setting it apart from traditional methods. The sensors can monitor temperature, stress/strain, humidity, light, sound, and various physiological parameters, making them suitable for use in medical tapes, wearable electronics, and artificial eardrums.
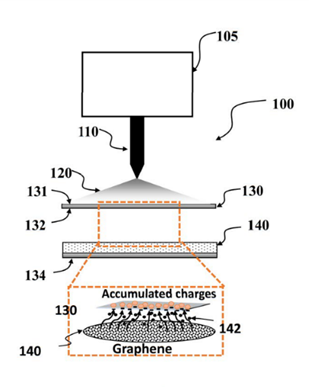
Exemplary printing system used to make a sensor.
(a) A non-contact printing system using electric fields to deposit conductive particles onto a thin film substrate with a plasma discharge device.
(b) The electric field allows precise and efficient particle adsorption, improving the manufacturing of printed sensors.
Desired Partnerships:
- License
- Sponsored Research
- Co-Development